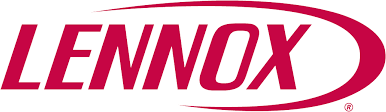
Plant Quality Assurance Manager
Lennox
- Orangeburg, SC
- Permanent
- Full-time
- Overseeing the development of quality standards and protocols for quality assurance testing models.
- Overseeing sampling procedures, techniques, and equipment.
- Developing techniques for ensuring the maintenance of quality levels throughout the production process
- Maintaining a continuous inspection, testing, analysis, and problem resolution process to ensure quality standards can be met on a continuous basis.
- Responsible for the detection of quality variances. Will recommend actions needed to achieve and maintain established quality levels.
- Ensuring projects are completed on time and within budget.
- Leading the Quality team, focusing on talent development, performance management and succession planning for key positions within the department
- Conferring with customers to define and resolve product quality problems. Develops the economics of any quality program.
- Reviewing product designs and recommend revision of specifications.