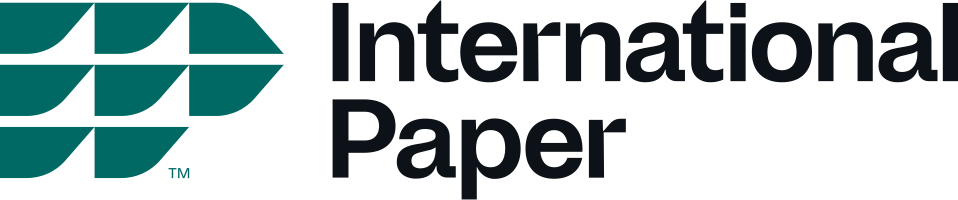
Area Process Manager Paper
International Paper
- Cayuga, IN Newport, IN
- Permanent
- Full-time
- Primary responsibility for leading PM.
- Leads efforts in key focus area including safety, production and cost efficiencies, reliability, team member engagement, and environmental, to achieve or exceed targeted performance.
- Lead the area to operational excellence through superior manufacturing techniques, application of ME tools and principles, total quality principles, and application of IP's Reliability Roadmap tools.
- Provides leadership and resources to support engagement and a high performance work team.
- Ensure development and implementation of manufacturing systems; including use of sustainability tools such as Trouble/Cause/Correction (TCC) and Centerlining.
- Help develop, demonstrate and support an organizational culture based upon values of empowerment, high involvement, and participative work force in a customer and quality focused organization.
- Lead a total quality management process, which will assure the highest quality production and customer standards, which meet environmental requirements.
- Develops, maintains, and uses sustainable methods for all processes and improvements.
- Manages team members in the mill as necessary to minimize downtime and maintain quality, and sets clear expectations holding team members accountable for meeting them.
- Maintains and develops team relationships.
- Participate in the development of the budget and capital plan processes for area.
- Lead area efforts in year-over-year cost improvement and supports the development and implementation of associated projects.
- Ensure team member relations, efforts and processes are in place that maximize motivation and the desire to work at Newport.
- Communicate and lead the application of facility policies and standards.
- Leads team members in goal setting and performance management consistent with company and mill direction.
- Coordinate daily operations between shift teams with a focus on process optimization.
- Help prioritize daily and scheduled shutdown maintenance.
- Work with suppliers to form good partnership relations and maximize TCO value.
- Coach safety in others and leads by example.
- Champions safety efforts by modeling and maintaining an environment of safe work practices and proactive approach to safety management.
- Champions and fullfils area specific 5S Expectations (5 Minute 5S Checklists Replenishment of tools and supplies, 5S Audits, etc).
- Understand and meets internal and external customer requirements.
- Develop, maintain, and use reliable methods for all processes and their improvements.
- Maintain and develop team relationships.
- Manage the communication efforts to support all of the above.
- Must be able to wear all required safety equipment.
- Noise levels in excess of 90 dB.
- Heat in excess of 100°F occasionally.
- Working environment is 24/7-ability to be on-call as need and/or required.
- Ability to work on concrete, and periodically move equipment/tools weighing up to 50lbs
- Previous team leader/supervisory, project management, etc. experience in the paper industry (two to five years).
- Experience in working with Maintenance and Engineering in Optimization projects and work orders.
- Proven ability to develop others.
- Proven record of leading safe work practices.
- Experience in setting good manufacturing practices and developing administrative and operative systems, including area goals and budgets, using the appropriate, reliable and sustainable methods.
- Ability to fully utilize and build partnerships with external resources like IP Technology and suppliers.
- BS in Science or Engineering.
- Experience working in High Performance Work System.
- Leadership experience working in a quality focused environment
- Knowledge of and leadership in paper mill safety practices.
- GreenBelt Certification
- Microsoft Project knowledge