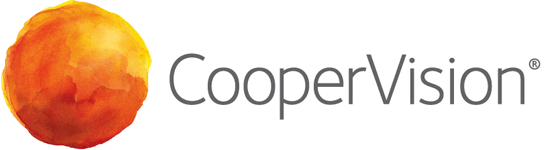
Process Flow Lead-Journey Worker-HV
CooperVision
- Juana Díaz, PR
- Permanente
- Tiempo completo
- Assure Manufacturing Area personnel perform their duties with high sense of Quality Awareness
- Identify area disciplinary situations.
- Provide feedback to the associate.
- Elevate situation to area manager or leader for consequent investigation.
- Assure all Manufacturing Area resources are available and within compliance;
- Human resources are certified in their respective operations.
- Area required equipment is operational.
- Area equipment is in compliance with its calibration/PMs
- Area operational supplies are available.
- Coordinate associates vacation plan
- Assure all manufacturing products are sent to sterilization area
- Assure production goals are achieved.
- Monitoring area daily production performance
- Perform safety daily monitoring Audits.
- Generates accidents / incidents reports as needed.
- Ensure correct resources are acting upon the situation of an equipment repair
- Ensure support of correct resources within shift to perform the repair is granted
- Assure Manufacturing Area information flow
- Coordinate and perform regular communications meetings
- Promote a good Work Environment
- Monitor Shift Performance
- Balance the work load among the area personnel using line balancing concepts
- Monitoring and maintaining ROLES Program within job area.
- Perform and documents periodical audits based on audit schedule.
- Promotes 6S methodology within associates.
- Suggest improvements.
- Provides audit findings, create actions and complete.
- Certifies that assigned associates obtain the technical, operational and product knowledge required to ensure that all manufacturing systems operate at optimal levels.
- Implement Corrective/ Preventive Actions
- Identify resources availability for Manufacturing Operation
- Coordinate special production meetings.
- Determine human resources requirements by roles.
- Execute Manufacturing operations as per applicable SOP's
- Manage Safety & Emergency issues.
- Implemented Safety corrective actions.
- Measure Safety shift indicators
- Improve Safety shift indicators.
- Identify process equipment not performing as expected.
- Communicate process capabilities and goals for Manufacturing operations.
- Ensure correct resources are acting upon situation for Equipment Repair
- Generate work order.
- Variance monitoring
- Identify causes.
- Identify and recommend opportunities.
- Influence and recommend actions to re direct.
- Identify optimization initiatives.
- Support all activities related to inventories reconciliation.
- Perform Lot Document Spot Screenings
- Identify Corrective/ Preventive Actions
- Create safe conditions by design.
- Continuous education of shift members in Safety
- Ensure completeness of shift investigations of accidents
- Identify possible causes of variation/ failure/ under performance for Manufacturing Operation.
- Monitor mean time between failure for spare parts and breakdowns.
- Analyze through a structured approach to identify root causes.
- Define and prioritize Process KPIs for improvement.
- Select KPIs to improve.
- Define the process to be improved by mapping the process flow.
- Improve Process KPIs performance.
- Create innovate and permanent solutions using technology and methodology.
- Develop and deploy implementation plan.
- Coordination and Execution of improvement plan, including validation.
- Identify Opportunities for Improvements in Equipment Performance
- Monitor Unit Performance
- Monitor Unit Performance Indicators
- People Performance Appraisals & Feedbacks
- Coordination Overtime for Non- Exempt