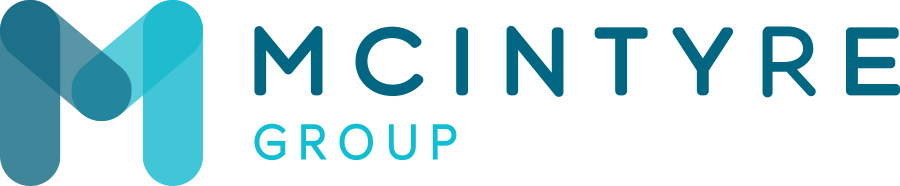
EHS Specialist
The McIntyre Group
- Eminence, KY
- Permanent
- Full-time
- Develop, implement, and maintain safety programs, policies, and procedures in compliance with regulatory requirements and industry best practices.
- Conduct regular reviews and updates of safety protocols to address emerging risks and promote a culture of safety.
- Provide safety training and orientation to new employees, contractors, and visitors on workplace hazards, safety procedures, and emergency protocols.
- Conduct refresher training sessions and toolbox talks to reinforce safety awareness and promote safe work practices.
- Conduct regular inspections and risk assessments of the workplace to identify potential hazards, unsafe conditions, and unsafe behaviors.
- Investigate accidents, near misses, and safety incidents to determine root causes and implement corrective actions to prevent recurrence.
- Ensure compliance with all relevant safety regulations, standards, and codes by monitoring workplace practices and activities.
- Coordinate with regulatory agencies and external auditors for inspections, permits, and certifications as required.
- Promote safety awareness and encourage employee involvement in safety initiatives through effective communication channels, such as safety bulletins, posters, and newsletters.
- Establish open lines of communication for reporting safety concerns, near misses, and incidents, and facilitate timely resolution of issues.
- Develop and implement emergency response plans, including evacuation procedures, fire drills, and first aid protocols.
- Organize and participate in emergency response drills and exercises to ensure readiness and effectiveness of response procedures.
- Serve as a liaison between management and employees on safety matters by participating in safety committee meetings and facilitating discussions on safety-related topics.
- Collaborate with cross-functional teams to address safety concerns and implement safety improvements.
- Education: Bachelor's degree in Occupational Health and Safety, Environmental Health, Industrial Hygiene, or a related field. Certification in Occupational Health and Safety (e.g., CSP, ASP, OHST) is desirable.
- Experience: Several years of experience in occupational health and safety roles, preferably in a manufacturing environment.
- Knowledge: Comprehensive understanding of occupational health and safety regulations, standards, and practices, including OSHA, EPA, and NFPA requirements.
- Communication Skills: Excellent verbal and written communication skills to effectively convey safety information and instructions to employees at all levels.
- Problem-Solving Abilities: Strong analytical and problem-solving skills to assess risks, identify solutions, and implement preventive measures.
- Interpersonal Skills: Ability to build rapport and collaborate with employees, management, regulatory agencies, and external stakeholders to achieve safety objectives.
- Attention to Detail: Diligent attention to detail and accuracy in conducting safety inspections, audits, and investigations, and documenting findings and recommendations.
- Computer Proficiency: Proficiency in using safety management software, databases, and Microsoft Office applications for data analysis, reporting, and record-keeping.